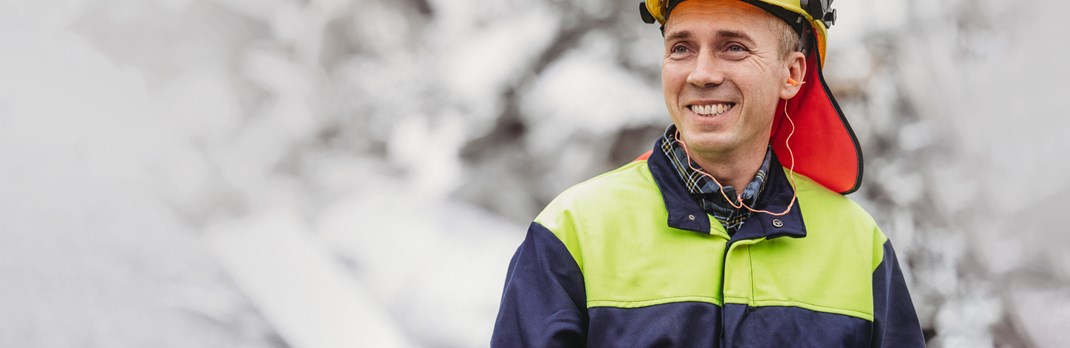
Sustainable operations
Gränges’ plan for sustainable operations is focused on resource efficiency (energy, water, waste), workplace safety, sustainable workplace, and ethical business practices. A strong focus is to strengthen operational efficiency and enforce a safety-first culture.
3.5 MWh/tonne
total energy intensity
10.1 TRR
number of recordable accidents per millions hours worked
Transitioning to renewable electricity by 2030
Gränges aims to use 100 percent renewable electricity by 2030 to reduce its climate impact. The company actively explores long-term partnerships through Power Purchase Agreements (PPA) to increase renewable electricity usage. In 2023, significant progress was made, with the Shanghai facility converting to 100 percent renewable electricity, and Gränges Americas expanding its partnership with Entergy to increase solar energy usage at the Newport facility. Solar panels were also installed on the roof of the Shanghai production facility, generating renewable electricity that powers both the facility and the local community.
Improving energy intensity
Gränges focuses on improving energy efficiency in its production processes to reduce scope 1+2 emissions and energy costs. Digital tools are used to identify areas where energy savings are possible, such as improving metal yield and optimizing thermal processes. The goal is to reduce energy intensity by 17 percent by 2025 compared to the 2017 baseline. In 2023, energy intensity increased by 7 percent versus 2017, primarily due to higher energy usage for remelting a greater volume of recycled aluminium.
Phasing out fossil fuels
To transition to net-zero fuels by 2040, Gränges is working to phase out fossil fuels used in production. This shift is challenging, as current decarbonization technologies are still being developed and remain costly. The company is investigating alternative energy sources, such as biofuels, and has already implemented oxyfuel burners at its Finspång facility. Gränges continues to explore options to reduce scope 1 emissions and invest in technologies to decarbonize production.
Pollution control
Gränges ensures compliance with environmental permits by conducting regular maintenance and annual measurements at all facilities, in line with local legislation. Emissions are actively reduced through the installation of monitoring systems and bag house filters, with air wash systems used in Huntingdon and Finspång to recover mill oil and reduce TOC and VOC emissions. In 2024, a new gas purification system was installed at Finspång to further reduce oil emissions. Gränges’ Global Environmental Policy guides efforts to reduce pollution, protect biodiversity, and phase out hazardous materials. While no global targets exist, local authorities regularly monitor emissions to ensure they remain within acceptable limits, securing the company’s continued operational license.
Water Management
Gränges primarily uses water for cooling production equipment to prevent overheating and production disruptions. Water management is handled based on local circumstances, as the production sites are located in areas with varying water stress and risk. The company aims to implement local water management plans at all facilities by 2025. These plans will include local targets and activities to address water-related impacts, such as improving water efficiency, effluent discharge quality, conservation efforts, and local stakeholder engagement. By the end of 2024, Gränges had implemented local water management plans at three sites: Finspång, Newport, and Shanghai. The Newport site is certified in accordance with the Alliance for Water Stewardship’s (AWS) International Water Stewardship Standards.
Gränges works to continuously improve the working environment as well as health and safety awareness and behavior. Occupational health and safety (OHS) management systems are implemented in all production facilities in line with local legislation, with the objective to proactively and quickly remove safety hazards and to drive safe behavior. Gränges’ goal is to reach a Total Recordable Rate (TRR) of 3.0 and a Severity Rate below 50 by 2025.
Key risks areas
Gränges has identified six key safety risk areas in operations: mobile equipment, fire suppression, machine safety and lock/ tag/verify, molten metal, confined space, and fall protection. Global Standards have been developed and rolled out for each risk area, including minimum requirements that all Gränges’ facilities have to implement. All regions have appointed a subject matter expert (SME) for each identified key risk area to ensure continuous improvement and implementation of risk mitigating activities.
Actions to improve physical safety and to foster a safety culture. To improve the physical safety environment, Gränges has installed guard rails and pedestrian access gates walkway. Gränges has also upgraded its cranes and fire protection systems, as well as equipped its forklifts with red lights marking the danger zone.
To increase safety awareness and foster a safety culture, Gränges provides annual health and safety trainings for employees, temporary staff, managers, and onsite contractors. Further, Gränges conducts internal cross assessments where regional safety representatives visit the production facilities to share learnings and provide feedback on safety improvements.
People and company culture are key to past and future success. Gränges aims to be the preferred employer in each location where it operates, and strives to provide a workplace where employees can thrive, realize their full potential, and contribute to developing a high-performing organization. Activities to attract and engage employees are driven by a people plan for each region, with clear targets and regular follow-up.
Gränges’ cultures and values
In 2023, Gränges launched an updated set of core values – sustainable, action oriented, and committed. The core values guide employees in their daily actions and lay the foundation for how to conduct business responsibly and ethically.
Talent and leadership development
Good leaders are of the utmost importance to remaining successful over time. Gränges has a structured process for working with talents and aims to develop one of the best talent programs in the industry for managers, senior managers, and key experts. Mentorships and job rotation are important factors in addition to leadership training.
Investing in the team
Gränges offers a competitive compensation package, but also prioritizes a good social and physical work environment, continuous training, and interesting development opportunities for its employees. In addition, employees are provided with occupational health services both on and off site, including flexible work options, wellness grants, and regular health checks. Gränges follows up on employees’ general motivation and wellbeing via the annual performance and development discussion. The company also conducts employee surveys every two years to track status.
Promoting an inclusive workplace
Gränges is committed to being an open and inclusive employer, with zero tolerance for discrimination. Diversity aspects include gender equality as well as ethnic diversity, where the latter is mainly applicable for Gränges Americas. Gränges aims to expand the diversity of its work force which is an important aspect to attract and retain employees, but there are challenges to do so. This includes cultural aspects, shift work, a flexible job market, and the geographical location of the production facilities.
Gränges is committed to running its business in an ethical and responsible way and being an ethically sound partner in all its relations and in the societies in which the company conduct business. Gränges’ Code of Conduct outlines the company’s ethical principles and is based on international standards on human rights, labor conditions, the environment, and anti-corruption, including the UN Global Compact and its ten principles.
Counteracting corruption
Gränges’ Anti-Corruption Policy provides an overview of Gränges’ anti-corruption principles and explains the basic legal and ethical requirements that shall be followed to avoid corrupt practices throughout business activities conducted for Gränges. Gränges has zero tolerance and will always act rapidly, stringently, and vigorously if discovering corruption or unethical behaviour as it can prevent economic development, distort competition, increase costs, and damage confidence and reputation.
Global ethical trainings
To ensure effective implementation of the Code of Conduct and the Anti-Corruption Policy, Gränges conducts annual trainings which covers all employees, the Board of Directors as well as contracted workers. The trainings combine facts and guidelines with practical ethical dilemmas to increase the knowledge of how to act in specific situations and are updated annually. In 2023, Gränges reached a 100 percent completion rate in both trainings.
Whistleblower Function to detect misconduct
Gränges has an externally managed Whistleblower Function that aims to detect irregularities that may seriously harm Gränges’ business or employees. The function is available for Gränges’ employees and business partners on the company’s website, intranet or by phone and information can be provided anonymously without the fear of retaliation.
100%of employees participated in Gränges' Code of Conduct-training |
100%of white-collar employees participated in Gränges' Anti-corruption training |
A trusted member of our local communities
Gränges has a deep engagement in the local communities where we operate. Our role goes beyond being an attractive employer; we actively engage in building and supporting a strong and resilient society. By supporting education, sports and wellbeing, cultural events, and charitable causes, Gränges strives to be an active and trusted community member.
Education and social welfare in focus in Europe
In Finspång, Sweden, Gränges sponsors Curt Nicolin Gymnasiet (CNG), an upper secondary school, to which Gränges offers internships and summer jobs for students. Gränges also supports multiple local sport associations and other educational initiatives. By being the main sponsor of the annual business day in Finspång (sv: “Stora näringslivsdagen”), Gränges contributes to strengthening the local business development.
In Konin, Poland, Gränges is involved in various fund-raising activities for social welfare, such as the Pass It On Foundation “Podaj Dalej ”, a foundation focusing on helping people in need. Gränges also supports a charity run, engages in local job fairs, and supports a family support center to assist families that face various challenges.
Volunteering central in Americas
In the U.S, Gränges sponsors the Cheerwine Festival in Salisbury where the company engages with the community about our career opportunities. The company also volunteers at the GraceWorks facility in Franklin, focused on donations to citizens in need. Gränges also offers support to schools, sponsors local sports teams, and engages in several local volunteering days throughout the year.
People and environment drive engagement in Asia
In Shanghai, Gränges volunteers in middle school teaching activities in Yun Nan organized by Shanghai Foreign Investment Association. Gränges also participates in local tree planting in Jia Ding Industrial Zone. The local community support also includes activities for the elders, such as the Chong Yang Festival.