The Shanghai team made the impossible possible
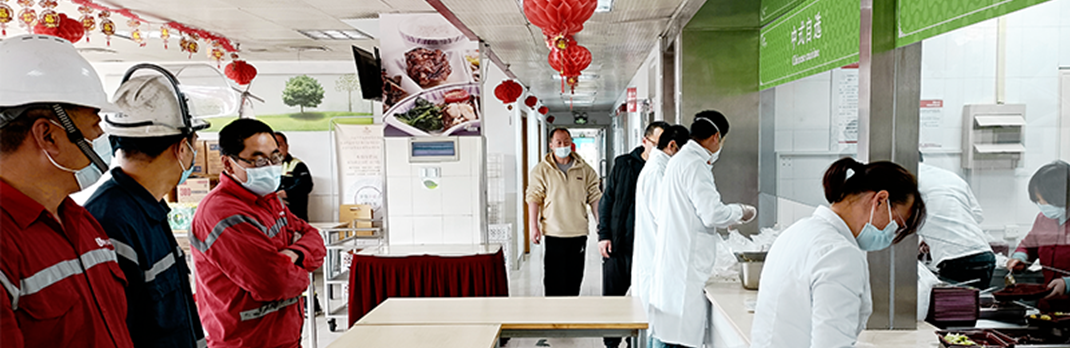
An extraordinary effort was made by the employees at the Shanghai production site in spring 2022. While Shanghai city was in complete lockdown employees volunteered to work and live at the site to keep the production going.
Customer success and employee wellbeing
CunXian Yue, SVP Operation Asia, gives his view.
What made you stay at the site?
We were fully booked at first half of the year and our customer had full production. A stop in our production would give us a big challenge for a long period.
How did you work to get your employees to volunteer?
We had a thorough review and open communication with our employees. Luckily many of our employees were willing to support Gränges. To be considered as a volunteer you needed to be free to leave home without quarantine and it should not impact the family negatively – children or old parents. Our commitment to our employees was to offer a balanced workload. Around half of the workforce decided to volunteer.
What challenges did you face?
Initially, we planned for two weeks but ended up with a lockdown that lasted for over two months. The uncertainty of the time span was of course a challenge psychologically for us and our employees. Furthermore, to prepare for decent accommodation to be able to have a good sleep and privacy. From a production perspective we had a logistical challenge since transports in Shanghai were limited, both for receiving raw material and delivering our products to customers. We need good communication internally and externally and a lot of creativity and drive in these situations!
How did you manage to live a decent life for over two months?
We got the special permission from the authorities to allow the canteen service to be open. It was important to engage in other things than work, so we arranged sports activities and competitions in football and basketball. Luckily, we already had such facilities on the site. We also gave extra support to employee families to get food, such as gift packages of meat, rice, egg and vegetables.
___________________________________
Coming out stronger as a team
Albert Zhang, EHS manager Asia, reflects on the period.
What were the toughest challenges for you from a health & safety perspective?
That was to make sure each person had a good mental well-being. As responsible for EHS at the production site I had to deal with things we never have faced before, including living conditions, epidemic prevention supplies, support to government in organizing covid tests and ensuring a good work life balance. We had to create a safe and socially stable working environment.
What was your recipe for succeeding?
I believe it was a lot about daily communication with the employees and teams. Being there, listen, take immediate actions to improve and arrange games and other activities. We got an unexpected achievement by having one common goal and sharing common values. The challenge became a successful team effort where we all believed we must be able to overcome all sorts of issues. I feel honored and lucky to be part of this team!
To conclude CunXian Yue reflects on results and learnings:
I would say that we made an outstanding effort! We ended up with zero interruptions and infection cases of the volunteers. We kept 70 days of sustainable operation successfully and in October we finally reached record high volume which exceeded expectations. Our cross- functional meetings for fast communications and quick decisions made it possible to keep flexibility to prioritize customers’ orders.
We can conclude that we have a strong company culture, great management team, loyal employees and excellent teamwork inside and outside the plant together. All these factors make the difference! We are proud of our achievements as a whole team and got many valuable experiences. This will make us more confident when we face new challenges.