Sustainability
By managing its business in a sustainable way, Gränges strengthens its long-term competitiveness and creates financial and operational value for the company and its stakeholders. Gränges has an ambition to develop industry-leading aluminium solutions that can help its customers and end-users become more sustainable. To achieve sustainable growth, Gränges will focus on investing in three areas: sustainable supply and recycling, sustainable operations and sustainable customers and sectors.
Our strategic focus areas
Discover
Sustainability news
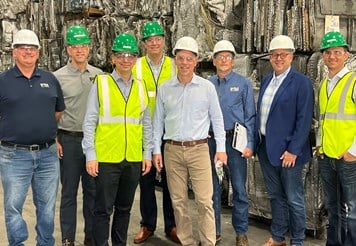
Gränges expands sustainability efforts with dual recycling partnerships
Gränges has taken significant steps towards its 2040 net-zero goal through two strategic partnerships that underscore its commitment to sustainable aluminium solutions. These collaborations focus on recycled and low-carbon materials, advancing...
Read more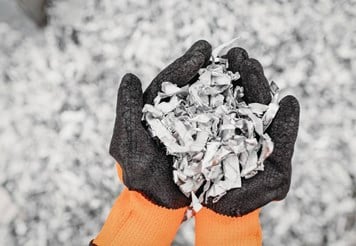
Gränges maintains Leadership level in CDP’s climate rating
Gränges has in 2025 retained its A- rating from CDP, demonstrating its “Leadership” level in climate change disclosures. This recognition highlights the company´s ambitious sustainability plan and commitment to transparency in sustainability and...
Read more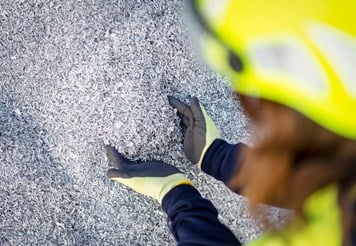
Strengthening our sustainability journey with the First Movers Coalition
In a strategic move to reinforce its commitment to sustainability leadership, Gränges joined the World Economic Forum’s First Movers Coalition (FMC) in 2024. This membership strengthens the company’s position in driving the aluminium industry’s...
Read more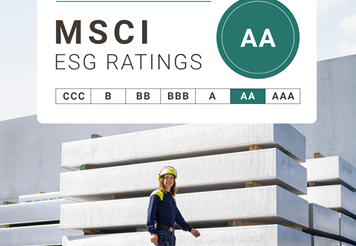
Gränges retains AA rating from MSCI for the fifth consecutive year
Gränges has once again retained its AA rating from MSCI, marking five consecutive years at this high level. This places Gränges among the top 11% in the Metals and Mining – Non-Precious Metals industry, reinforcing the company’s position as a...
Read more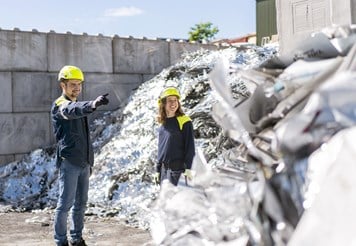
Gränges supports advance recycling in Tennessee, USA
Gränges is strengthening its commitment to sustainability by collaborating with industry leaders and policymakers to drive recycling initiatives in Tennessee, USA. By engaging with key stakeholders and supporting industry-wide efforts, Gränges...
Read more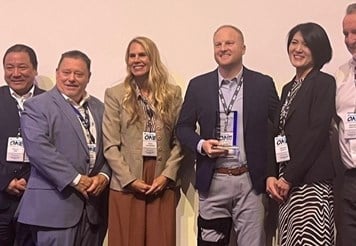
Gränges Americas recognized for sustainability excellence by Daikin
Gränges Americas has been honoured with Daikin's Excellence in Sustainability award at their Annual Supplier Meeting, held in November 2024. The award recognizes outstanding efforts in driving sustainability and transformation, and it marks the...
Read more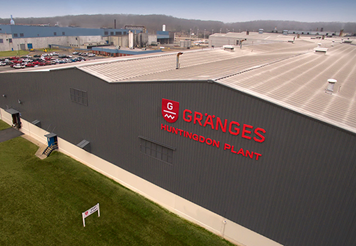
All Gränges Americas’ sites certified against ISO 50001
All three production sites in Gränges Americas are now fully certified against the energy management standard ISO 50001:2018 following a successful certification of the Huntingdon facility. Through this certification, Gränges will work to...
Read more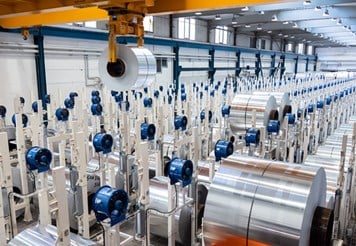
On the track towards sustainable transport solutions
Moving goods using responsible and low-carbon transport can make a big difference for the environment. Thanks to optimized transportation, Gränges has found ways to reduce emissions from its customer shipments, in some cases by as much as two...
Read more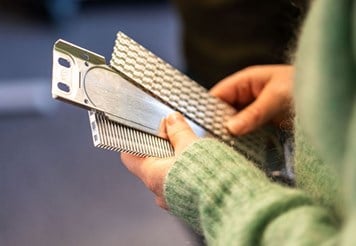
Third-party verified sustainability information available for all Gränges’ products
Since the end of 2023, Gränges can offer third-party verified carbon footprints for 100 percent of its products worldwide. This has been achieved through the implementation of internal life-cycle assessment and carbon footprint tools at all...
Read more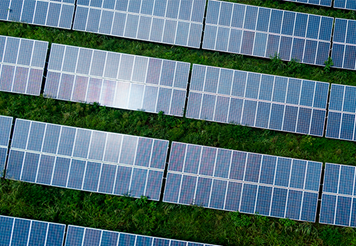
Gränges secures 100 percent renewable electricity in Newport
Gränges has taken another important step in its sustainability journey by securing renewable electricity for the operations in Newport. The site is thereby Gränges’ first of three US production facilities to reach 100 percent renewable electricity.
Read more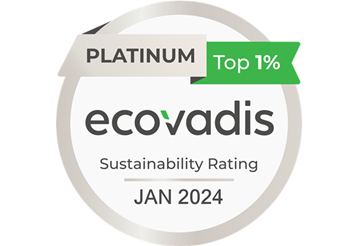
Gränges achieves renewed Platinum sustainability rating by EcoVadis
Gränges has for the third consecutive time been awarded a Platinum rating from EcoVadis, the largest independent provider of business sustainability ratings. Platinum is the highest rating, and it places Gränges among the leading one percent of...
Read more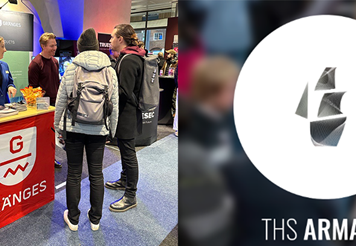
Gränges’ focus on sustainability opens up career opportunities
Last week, Gränges attended Sweden's largest student-run career fair - The Armada, at the Royal Institute of technology, KTH in Stockholm. During two days, we met with students from around the world, curious about us and what opportunities we could...
Read more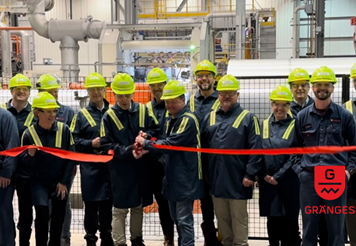
New recycling and casting capacity in Huntingdon fully operational
The new recycling and casting line in Gränges’ production facility in Huntingdon, Tennessee, will increase the capacity, lower cost and support Gränges’ high sustainability ambitions by improving both energy and carbon emission intensity.
Read more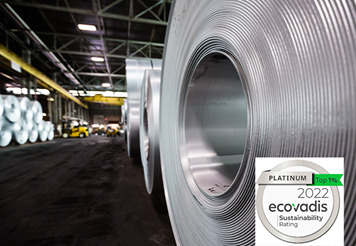
Gränges awarded EcoVadis Platinum rating for the second consecutive year
For the second year Gränges has been awarded a Platinum rating from EcoVadis, the largest independent provider of business sustainability ratings. Platinum is the highest rating awarded by EcoVadis and it places Gränges among the leading 1 per cent...
Read more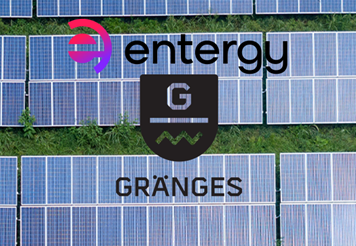
Gränges Americas in long-term partnership with Entergy to increase renewable energy in Newport
Gränges has signed a 10-year contract with the electricity company Entergy Arkansas for Gränges’ production site in Newport, Arkansas. Under the contract, Granges subscribes to approximately 25 percent of its capacity for the Granges’ Newport Site...
Read more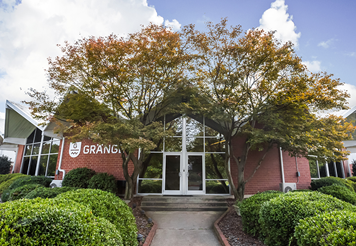
Gränges' production facility in Salisbury achieves ISO 14001 certification
As of August 25, 2021, the environmental management system at Gränges’ Salisbury site in the US has successfully been certified in accordance with the environmental management standard ISO 14001:2015.
Read more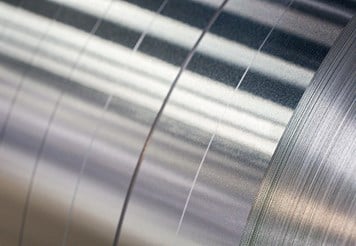
Gränges’ sustainability efforts recognized
For the third consecutive year, Dagens industri and Aktuell Hållbarhet in collaboration with Lund University School of Economics ranked this year's sustainable Swedish companies. Once again, Gränges was among the top-ranked material companies.
Read more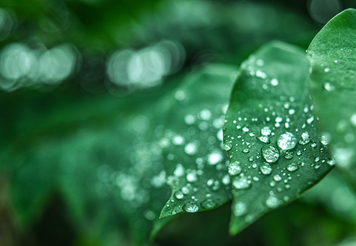
Gränges’ sustainability efforts gets higher ranking
For the fourth consecutive year, Dagens industri and Aktuell Hållbarhet in collaboration with Lund University School of Economics ranked this year's sustainable Swedish companies. Once again, Gränges was among the top-ranked material companies.
Read more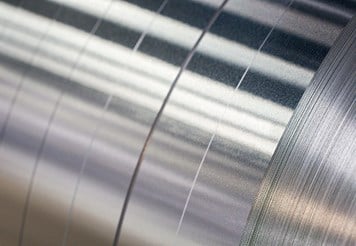
Gränges’ sustainability efforts recognized
For the third consecutive year, Dagens industri and Aktuell Hållbarhet in collaboration with Lund University School of Economics ranked this year's sustainable Swedish companies. Once again, Gränges was among the top-ranked material companies.
Read more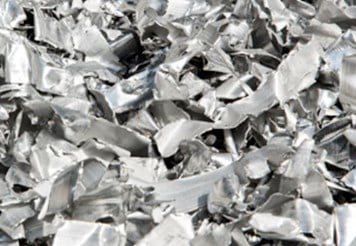
Energy savings – not a Scrappy project
To have good and sustainable solutions for energy consumption is very important for any manufacturing company. We talked to Paul Neutjens, Gränges’ SVP Process Engineering & Operational Development and the driver of Gränges’ Energy Savings Project.
Read more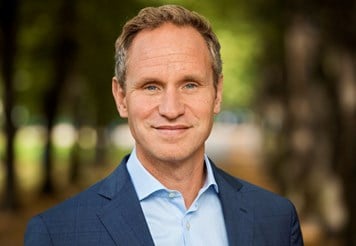
Sustainability main driver for material development
Every year, World Material Forum (WMF) organizes a conference in Nancy, France, where they invite senior CEO’s from different world leading industrial companies, politicians and academics to discuss material development. We talked to Gränges’ CEO...
Read more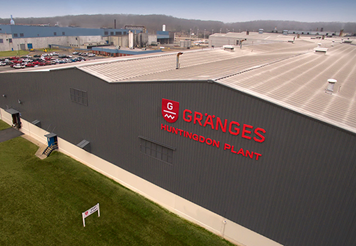
Gränges' production facility in Huntingdon achieves ISO 14001 certification
As of July 16, 2020, the environmental management system at Gränges’ Huntingdon site in the US has successfully been certified in accordance with the environmental management standard ISO 14001:2015.
Read more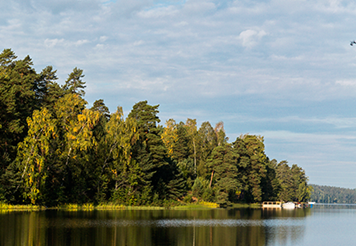
Gränges’ sustainability efforts recognized
The rating institute MSCI has recently upgraded Gränges’ ESG rating from A to AA. This is a very good recognition for the comany's sustainability efforts and puts Gränges among the top 6 per cent companies in the Metals and Mining sector...
Read more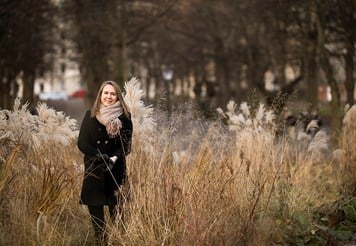
Connecting sustainability to business value
With the arrival of its new VP Sustainability, Gränges is stepping up its efforts to strenghten the company’s longterm competitive edge. Meet Sofia Hedevåg who is leading the group towards a more sustainable path to business value.
Read more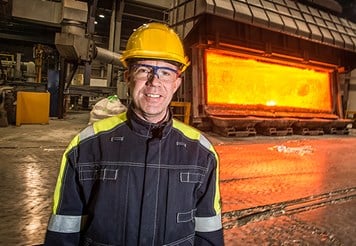
Energy consumption halved thanks to oxyfuel combustion
A halving of energy consumption, temperatures that are more even, and a better working environment. These are just a few of the results achieved at Finspång by using oxyfuel combustion rather than air combustion in the blast furnaces.
Read more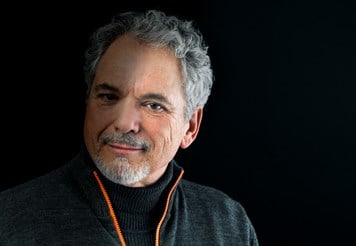
Can you braze with sustainable environmental concern?
Our focus on the environment impact and health & safety, is manifested through the continuous streamlining of production processes, and environmentally-conscious product development. As part of this work, we have developed TRILLIUM®, a composite...
Read more